
Workarounds for the Part Workbench and Part Design Workbench No.Ĭheck the geometric and mass properties of the model
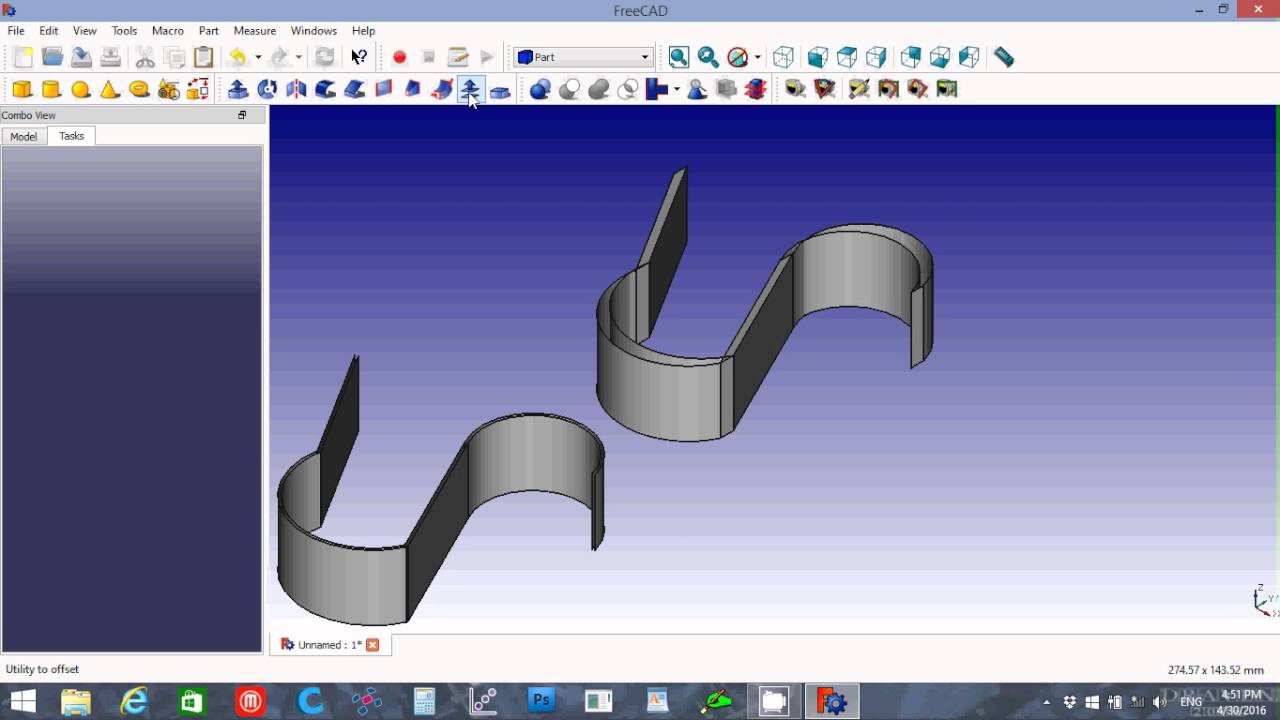
Create a radius dimension instead (you can enter the diameter divided by 2 - the calculation will be handled by FreeCAD).Use the currently available rectangle from 2 opposite corners and rectangle from center tools and apply proper constraints afterwardsĭiameter dimension with respect to a symmetry axis for revolved parts.Rectangle from 3 corners and rectangle from 3 points by center tools If the sketch is plane-parallel to one of the main planes of the global coordinate system: use Part SectionCut.Create a Link from the object, and slice that object to get actual cut edges.Projection of cut edges when making a sketch on a plane cutting through an object Use the Draft Workbench, but 3D drafts can't be converted to sketches (however, they can be used for spatial frame analyses done internally or externally, and for PartDesign AdditivePipe or Part Sweep paths).Project multiple edges at once with the External Geometry tool when a face is selected Manually trace over the geometry created by this tool.Possibility to use the results of the External Geometry tool directly for operations on the sketch Create a face from the sketch with Part MakeFace, then analyze that face with Part CheckGeometry.Apply tangency to endpoints instead of edgesĬheck geometric and mass properties of the sketch (area, center of mass, second moments of area and so on).Apply dimensional constraints after drawing the geometry.Input coordinates and dimensions on the go (when drawing an object) Use a range of dimensional constraints: 3 for lines, 1 for angles and 3 for arcs/circles.Apply an appropriate Sketcher ConstrainAngle constraint or drag a vertex of one of the objects.Optionally add constraints between the objects to be rotated.Remove constraints that prevent the rotation, e.g.
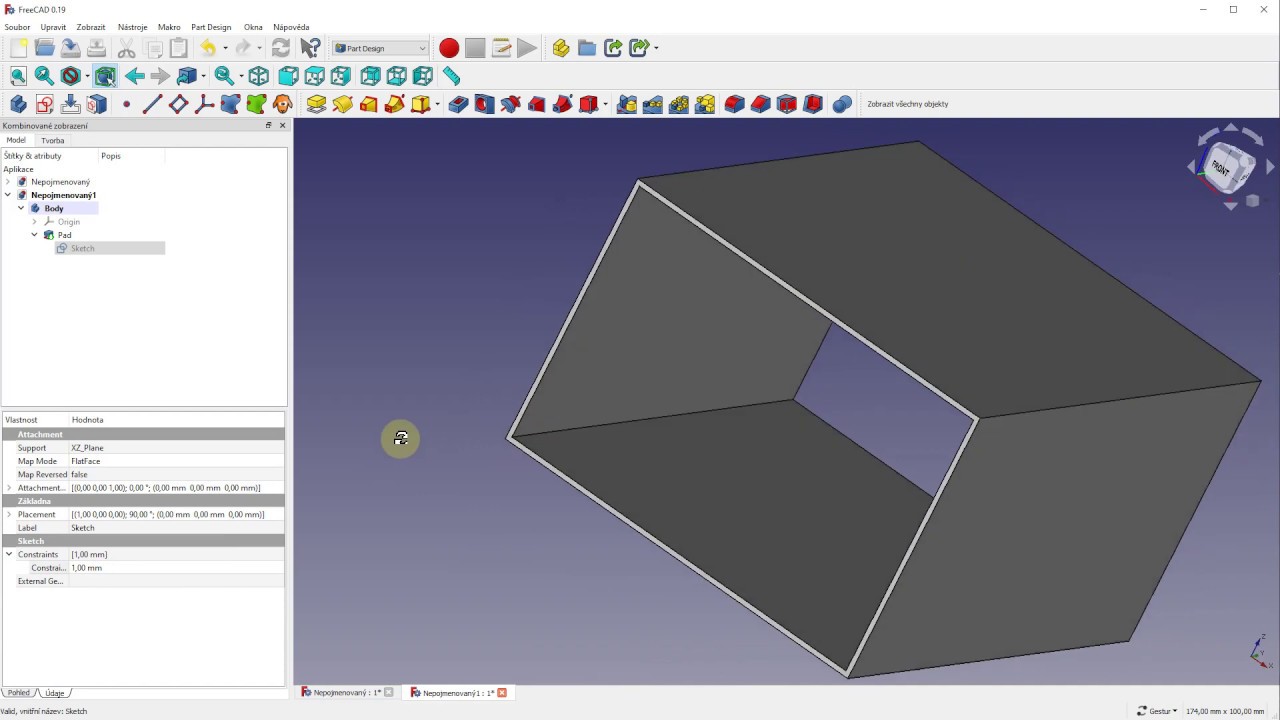
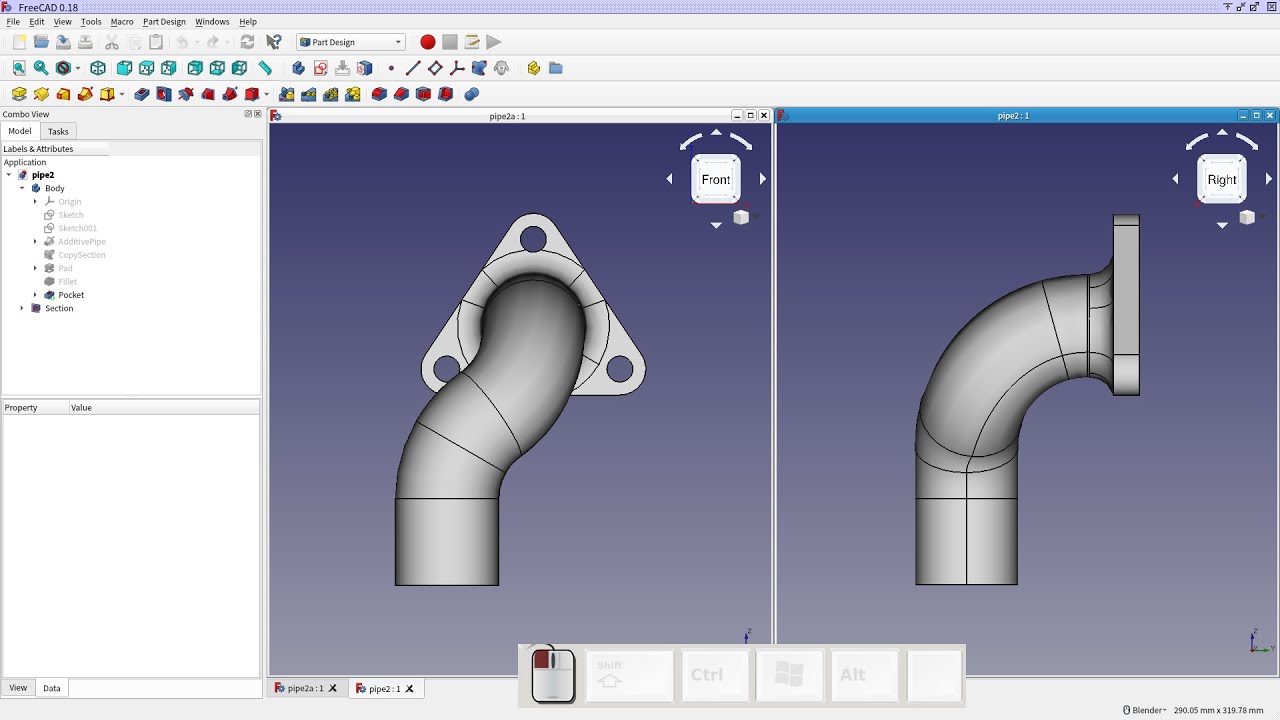

